Intrinsically Safe Ultrasonic Sensors
Designed for Hazardous Locations/Explosive Atmospheres
When continuous operation is critical, Migatron’s intrinsically safe ultrasonic sensors deliver. Designed for use in hazardous locations/explosive atmospheres, these sensors offer non-contact level and distance measurement in hazardous gas or dust environments classified as Zone 0, 1, 2, 20, 21, or 22 for ATEX/IECEx, and Class I, II, or III for C-UL-US when used with approved intrinsic safety barrier(s). Migatron’s Intrinsically Safe Ultrasonic Sensors support equipment operation in some of the world’s toughest environments and are known for unparalleled performance.
Engineered for Hazardous Areas
Approvals
Our lines of Intrinsically Safe Ultrasonic Sensors carry approvals for many locations and regions. They Include: ANZEx, ATEX, IECEx, & C-UL-US.
Safe, Non-Contact Operation
Ultrasonic technology eliminates contact with volatile substances—reducing corrosion, and maintenance downtime.
For Extreme Industrial Sites
Ideal for exploration platforms, refineries, mining conveyors, and pipeline terminals, our sensors resist temperature swings, dust ingress, and washdown conditions.
Compatible with Safety Barriers
Our ZSB-409A 3-channel zener safety barrier provides “ia” level of protection for all of Migatron’s RPS-409A-IS product lines.
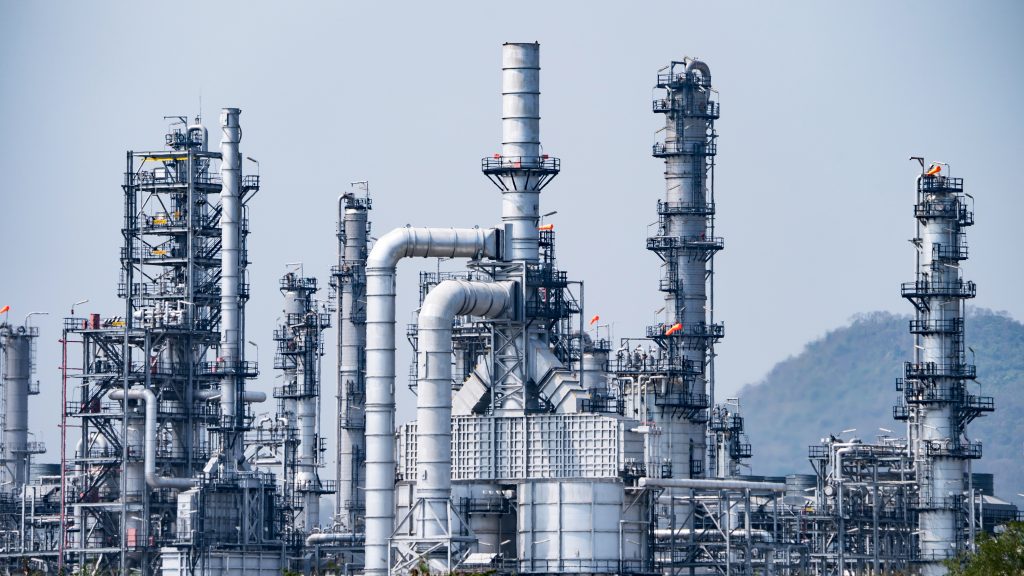
Benefits of Migatron Intrinsically Safe Sensors
- Certifications for Wider Use: Designed for international use in regulated industries with multi-agency approvals.
- Accurate Measurement Without Risk: Avoid process contact in explosive atmospheres, eliminating fouling and ensuring uninterrupted operation.
- Easy Integration: Analog outputs are compatible with PLCs, SCADA, and control interfaces in safety-rated environments.
Featured Intrinsically Safe Ultrasonic Sensors
Trusted in Oil & Gas and Mining
Designed for safe operation, Migatron’s intrinsically safe ultrasonic sensors are trusted by engineers and OEMs working in hazardous areas -above ground, underground,
and offshore.
Applications in Hazardous Areas
- Tank Level Monitoring in Refineries & Chemical Plants
- Distance Ranging on Mining Equipment
- Pipeline Integrity Monitoring Stations
- Offshore Platform Vessel & Bilge Monitoring
- Detection of Misalignment of the Conveyor Belt
- Cake Thickness Level
- Detecting anomalies that indicate tears or rips on a conveyor belt